Products & Services
Composite Alliance Corp has responded to the market demands for a greater variety of industrial processes and solutions to optimize the fabrication of composite components. Our capabilities range from engineering consulting, design, analysis, and first article development to manufacturing, industrialization, and product support in the following areas:
- Pre-forming:
- Automation solutions such as robotized preform cells and more
- Manual and automated cutting systems
- Pre-form compaction systems, drape forming, vacuum forming
- Mold design and fabrication for various applications such as compaction, polymerization, RTM, …
- Self-heating tooling for out of the autoclave curing, ideal for large composite structures.
- Press systems:
- Thermoset or thermoplastic composites, press/workstation and tooling
- Laboratory presses
- Automated injection and dispensing equipment capable of precise metering and mixing of one or multi-component thermoset or thermoplastics resins
- Handling/Rotation and demolding systems
- NDT equipment
- Machining/drilling equipment
By combining our areas of expertise and partnering with our customers to define the best processes, tooling and machinery for their needs, we are able to deliver superior value, reduce costs and optimize performance.
Automation Solutions
During the past decade many fast, cost-effective and advanced engineered preform technologies have been developed, allowing even complex 3D preforms to be created very fast. As a way to accelerate composite part processing through automation, Composite Alliance Corp is offering a variety of solutions such as robotized preform cells and pick & place systems, which can be integrated with a press/workstation.
Our robot-automated pick & place systems are tailored to customer needs, with the following advantages
- Cut & 3D positioning in the mold
- High productivity
- High degree of automation, minimizes hands-on labor required
More efficient molding process with shortest possible mold open time
Excellent quality resulting from to the repeatability of the robot
Our robotized preform cells allow for complete automation of the entire fabric preform process and are custom-designed according to customer specifications.
Cutting Systems
All composites manufacturers want to improve quality and productivity while reducing costs.
Automated cutting equipment can speed up production times and reduce labor costs. Composite materials can be cut into complex patterns, quickly, accurately, and with better edge quality. Cut materials can be marked to make part identification (and kitting) easier.
Composite Alliance offers a variety of cutting solutions to suit different cutting applications. We supply a comprehensive line of equipment ranging from manual cutting tables (with different cutting surfaces), to automated cutting systems or robotized fabric cutting stations; with the possibility to integrate additional Roll Stand, Pick-up & Place systems.
Our equipment is designed to cut the most diverse technical and industrial fabrics with precision while maximizing your productivity. A wide selection of widths, lengths and options are available for cutting either flat or 3D shapes such as after preforming or compaction, according to customer needs.
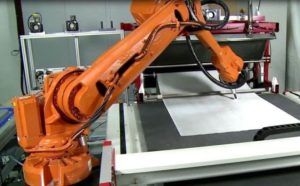
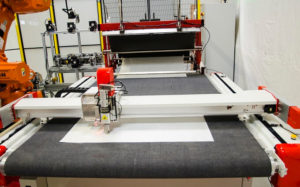
Compaction / Drape Forming Systems
The purpose of the compaction process is to control the material thickness and the fiber volume fraction prior to curing. There are many benefits to the compaction technique as, it removes trapped air between layers. It compacts the fiber layers for efficient force transmission among fiber bundles and prevents shifting of fiber orientation during cure. It reduces humidity, and finally it optimizes the fiber-to-resin ratio in the composite part.
Composite Alliance Corp proposes 2 main types of compaction systems:
- Mechanical / heat compaction
- Vacuum / heat compaction (table or trough)
All compaction equipment can be customized according to the preferred heating method, the chosen compaction process and the dimensions needed.
Molds
By taking advantage of the 36 years of experience of Techni-Modul Engineering – a recognized industry leader, expert in the design, engineering and manufacturing of molds – we are able to offer custom molds for various applications. Our experience working with CATIA CAD and with medium to large size tooling (up to 33 feet long) gives us the ability to successfully handle almost any kind of project.
According to the molding process requirements, the molds are made out of steel, invar, aluminum or composites. They can be autonomous and self-heated.
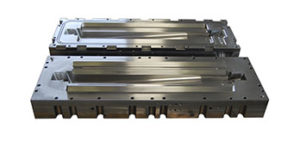
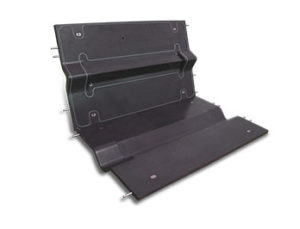
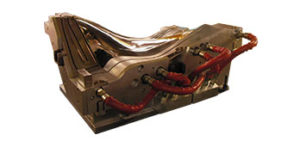
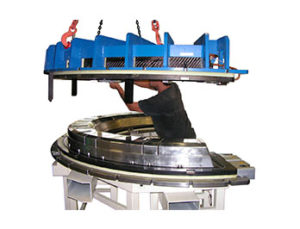
RTM, Prepreg & Thermoplastic Presses
Our line of advanced press systems can be designed for either laboratory applications or production optimization, for various composite molding processes such as Prepreg, Resin Transfer Molding (RTM) and Thermoforming. They provide easy accessibility for mold release agent applications, lay-up and cleaning of both upper and lower molds with 180° rotation opening.
A selection of standard presses is available, however most of our systems are usually custom made according to specifications, to attain the highest possible performance and efficiency. Our presses can be equipped with a choice of hydraulic, electric, pneumatic or mechanical clamping. The temperature regulation system can deliver homogenous temperature distribution with a selection between electric, water or hot oil heating. We offer our expertise in defining the best configuration for your press system as well as the integration of automation and periphery.
All of our workstations are supplied with a customized supervision interface able to:
- Generate and record process data reports and graphs, offer control and traceability of cure cycles and injection via PLC and computer software (Temperature, pressure, time…)
- Manage technical defects
- Automate all movements of the machines (structural, handling…)
- Make the work of the operators easier and safe
Laboratory presses
Injection & Dispensing Equipment
Composite Alliance Corp offers a comprehensive range of production & laboratory equipment for thermosetting resin processing applications (PU, EPOXY, silicone…). Thanks to our extensive expertise in metering and mixing, our machine can dispense from liquid to high viscosity resins for applications such RTM, VaRTM, C-RTM, Infusion. All units are operated from a PLC and/or Computer system and are configured according to customer’s specifications.
Our standard range offers :
One or two-component injection machine
Tank capacity : 10L to 30L
Operating temperature: up to 150°C (302°F)
Mixer : 15 rpm
Flow controlled (in flow control mode) : 300g/min max
Pressure controlled (in pressure regulation mode) : up to 10 bar (145 psi) or up to 25 bar (363 psi)
Automatic cleaning option
Supervision
Handling/Rotation/Demolding Systems
Large parts with complicated shapes may not be demolded readily even when mold release agents have been applied on the mold cavity. And depending on the material they are made of molds can be vulnerable to scratches and wear, and demolding tools in addition to other variables such as solvents or mold release agents may damage the mold surfaces. Caution should be used as well as the appropriate tooling and processes in order to prevent damage to both the demolded part and the mold. We have developed a line of special handling/rotation/demolding systems, designed to optimize these operations while reducing their overall cost.
Our demolding equipment is divided into 3 categories:
- Manual demolding
- Assisted demolding
- Automated demolding
Each system is engineered and manufactured to ease the demolding process with no damage to the composite part nor the molds, and is custom made according to each customer’s equipment line and products.

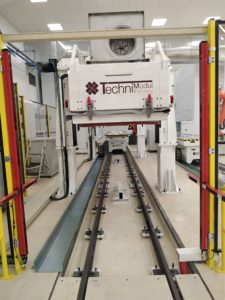
NDT Equipment
We supply Nondestructive Testing/Inspection equipment according to customer needs and applications.
Often, damage in composites is difficult to assess from just a visual inspection looking on the outside surfaces for matrix or fiber damage or dents. Nondestructive testing and inspection techniques are of great assistance when working with laminated composites where delamination and internal cracking are possible failure mechanisms. It can be used both for manufacturing quality assurance and for in-service damage detection, to inspect for damage without further damaging the composite structure or component. It is possible to determine both the nature and extent of any damage. In the aerospace industry where composites are used in many safety critical applications, NDT requirements are becoming increasingly important.
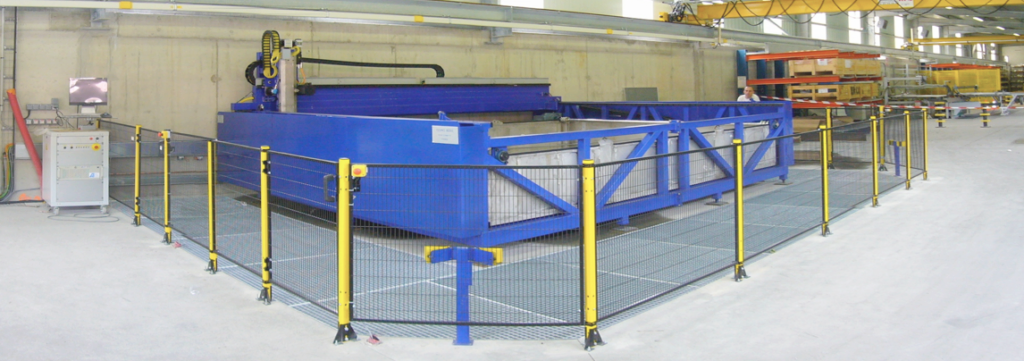
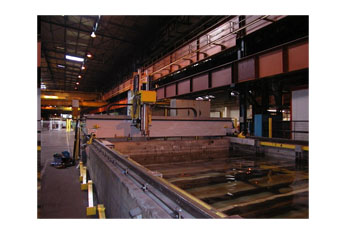
Machining / Drilling
Final contour machining might be necessary after the demolding of many composite structures and components. Machining composites, especially carbon fiber reinforced polymer (CFRP) material presents many challenges. The material is not homogenous because of the combination of plastic matrix with carbon fiber reinforcement and reacts not so predictably compared to monolithic metallic materials. Some common challenges are splintering/fraying due to high-strength fiber, the plastic matrix is sensitive to heat and can melt or risks of delamination in the structure.
Our experience in designing and manufacturing custom made composite machining equipment will help minimize your risks while getting the performance, efficiency and quality you desire. Composite Alliance Corp will help you define the right technology and tooling for your edge-trimming, drilling and surface finishing applications.